非均相臭氧催化技术的提升
非均相臭氧催化氧化催化剂
科力迩采用多种过渡金属氧化物((Mn2+,Fe3+,etc)为催化组分,通过大量实验及工程验证,优化各组分配比,开发出具有高适应性和催化活性的催化剂;采用多段精准温控烧结技术,优点是催化性能强、稳定性好、寿命长、有效减少使用过程中的流失率,防止二次污染;采用特殊造孔技术,形成高比表面积采用原子沉积技术对催化剂进行改性。
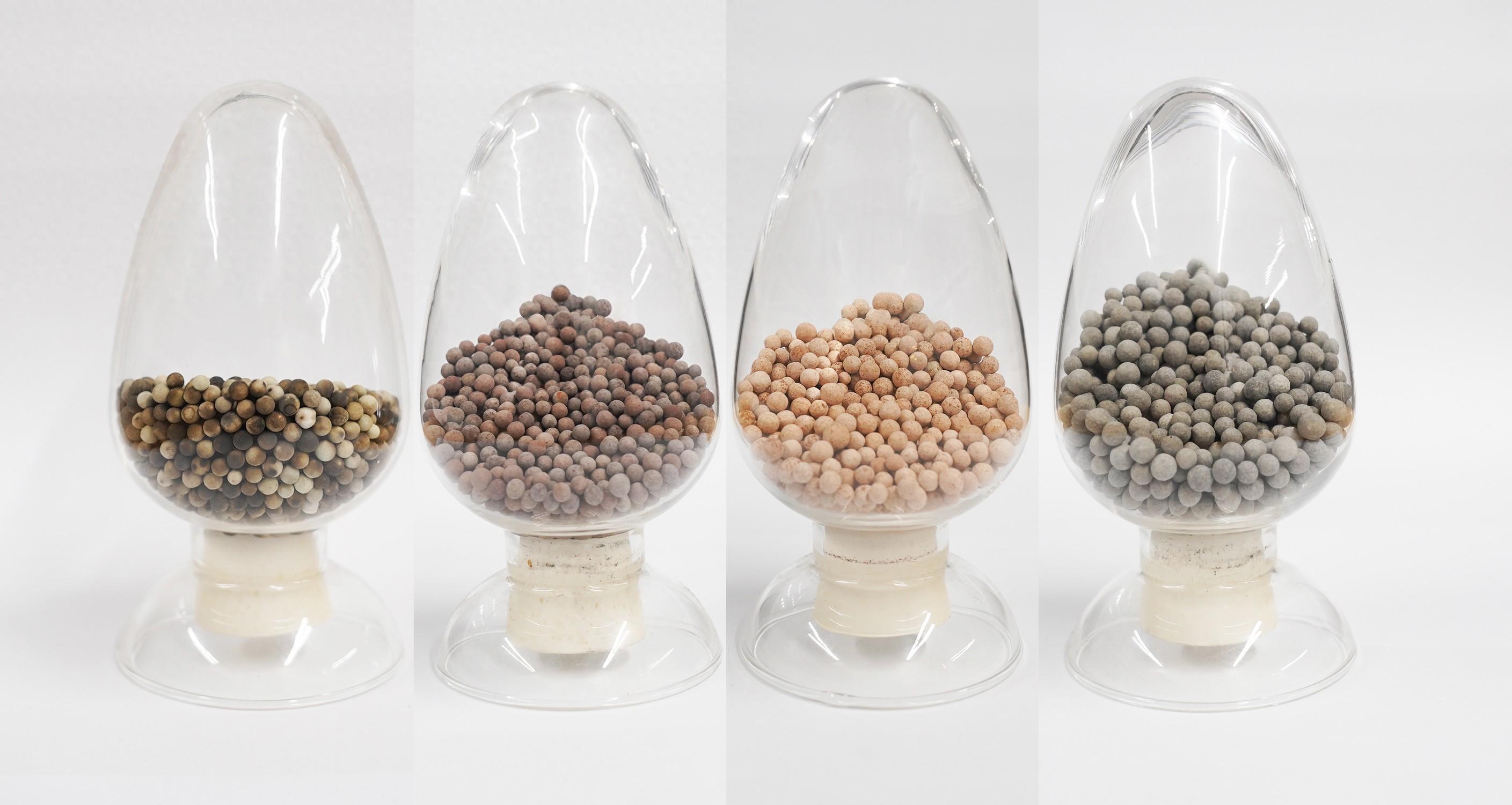
非均相臭氧催化剂
催化剂载体具有超亲水性,催化剂不易污染、结垢和堵塞,可长周期运行。催化剂可有效降低反应活化能,从而达到深度氧化,最大限度地去除有机污染物的目的。可加速臭氧在水中的自分解,增加水中产生的·OH浓度,从而提高臭氧氧化效果以及臭氧利用率,氧化效率比单纯臭氧氧化提高2~5倍。该复合催化剂的表征如下表所示。
水力空化技术
常规臭氧氧化工艺的布气方式为曝气盘曝气臭氧与废水在反应器底部混合发生反应残余的臭氧从顶部排放经尾气破坏后排放,出水由接触池上部溢流排放。臭氧直接氧化为主分解产生的·OH的能力较弱,对复杂的有机污染物降解速率较慢且氧化不彻底,通常需要投加过量臭氧使得工艺运行成本增加。
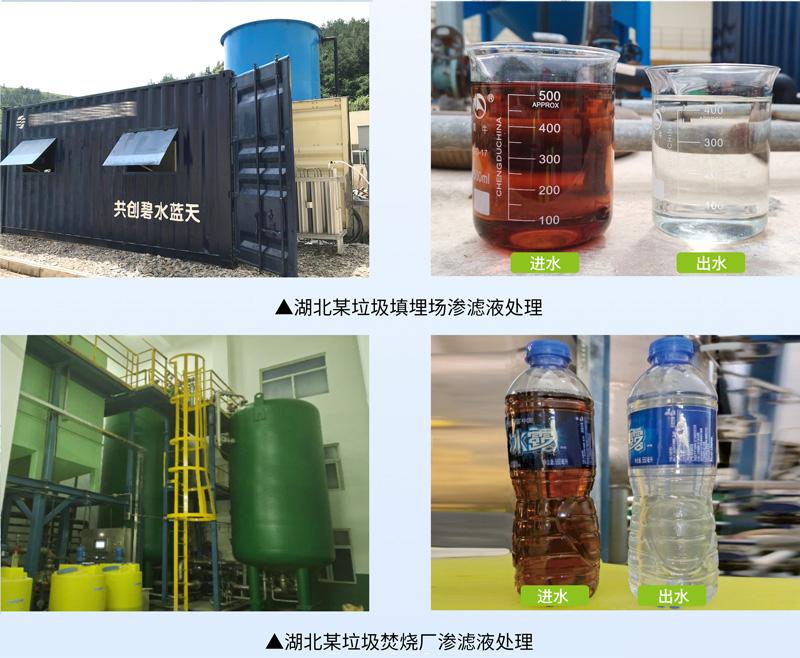
臭氧催化氧化工业装置应用
科力迩的专利技术将水力空化和臭氧氧化工艺相结合,利用高速湍流的液体增加了臭氧与污染物的接触机会,减小传质壁垒,使臭氧利用率提高;同时臭氧气体为空化泡的形成提供了更多的核,空化效果提高;在空化产生的高温、高压、高揣流的极端条件下臭氧分解产生更多的活性物质,组合工艺的氧化能 力显著提高。
微纳米气泡技术
一般定义其为直径<100 μm 的微米气泡与<1 μm 的纳米气泡,微纳米气泡可在溶液内做布朗运动,气泡会在液体界面内膨胀爆破或持久留存具有瞬时冲力,具有更高的传质效率。 气泡半径越小,比表面积越大且气体溶解得越快,传质效率高。自身加压溶解可以增强气液间物质转移能力,因此微纳米在水中的气体含量达到过饱和后继续气体输送过程并保持高效的质量转移效率。
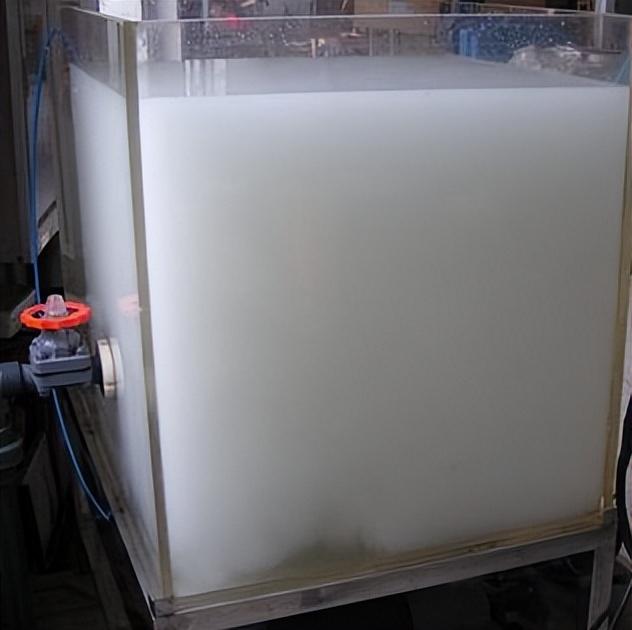
微纳米气泡效果示意
科力迩充分发掘微纳米气泡的优势,研发出一套以进口多相流动泵和专有微气泡发生技术微核心的微气泡生成系统;该系统产生的微气泡在水中停留时间长,降低了液体中的气体扩散。有学者利用电子自旋共振光谱验证,由于气液界面收缩时周围离子大量聚集,离子浓度显著升高,同时气泡坍缩时引起温度骤升,剧烈变化激发产生自由基。
综上所述,科力迩采用多种专利技术结合提升了非均臭氧催化氧化技术,经长期工业验证,非均相臭氧催化氧化技术在占地面积、投资和运行成本方面均占优,具有更高处理效能,适用于难降解工业废水的处理。