碳基臭氧催化剂介绍及其在污水处理中的应用
一、背景与需求分析
臭氧高级氧化技术在水处理中扮演着重要角色,它通过产生强氧化性的羟基自由基来分解水中的有机污染物。然而,单独使用臭氧时,其氧化能力受到限制,因为臭氧的直接反应速率较慢,且臭氧在水中的溶解度和稳定性不高。因此,引入非均相臭氧催化剂变得十分必要。这些催化剂能够提高臭氧的分解效率,从而增强氧化过程。
非均相臭氧催化剂是指在不同相态中工作的催化剂,它们可以是固体、液体或气体。在处理臭氧催化反应时,不同载体的催化剂具有各自的优缺点:
1. 金属氧化物基催化剂:这类催化剂通常具有较高的催化活性和稳定性,但可能面临成本较高和对环境敏感的问题。
2. 分子筛基催化剂:分子筛具有良好的热稳定性和选择性,但其合成成本较高,且在某些条件下可能失活。
3. 碳基催化剂:碳基催化剂,尤其是碳纳米管和石墨烯等碳材料,具有以下优势:
- 高比表面积:提供更多的活性位点,增强催化效率。
- 良好的化学稳定性:在多种化学环境下保持稳定,不易被腐蚀。
- 可调节的孔结构:通过改变碳材料的孔径和分布,可以优化催化剂的性能。
- 环境友好:碳材料来源广泛,制备过程相对环保。
- 可回收性:碳基催化剂通常易于回收再利用,减少资源浪费。
综上,以碳基材料作为载体的非均相臭氧催化剂具有显著的优势。碳基材料如活性炭、碳纳米管和石墨烯等,因其独特的物理化学性质,如高比表面积、良好的导电性和化学稳定性,使得它们成为理想的催化剂载体。这些碳基载体能够有效地吸附水中的有机污染物,并促进臭氧分子的分解,生成更多的羟基自由基。
二、碳基臭氧催化剂介绍
科力迩碳基臭氧催化剂(KHC-PC1001)
碳基材料广泛存在于自然界中,大多通过煤、生物质等燃料热解产生。在煤炭或生物质热解过程中挥发分的释放导致其内含大量孔隙结构,燃料中包含的大分子经过一次反应断键形成多种中间产物,这些中间产物经过二次反应生成最终产物。碳基材料表面一般含有丰富的含氧官能团,同金属基催化材料相比,碳基催化材料成本相对较低,具有较好比表面积、发达的孔隙结构,具有优良的吸附能力。同时,其发达的孔隙结构和高比表面积能够为活性催化组分的负载提供空间和表面支撑。
科力迩选用碘值1100以上,比表面积1400m2/g的活性炭为基质制备出一种高活性的非均相臭氧催化剂——KHC-PC1001,其微观结构如下图所示。其具有的高比表面积为催化反应提供了更多的活性位点,在多种化学环境下都表现出良好的稳定性,这使得该型碳基臭氧催化剂在酸、碱和有机溶剂中都能保持较好的催化性能。碳基臭氧催化剂还具有优异的电子传输能力,这有助于加速催化反应中的电子转移过程,同时碳基臭氧催化剂毒性较低,且材料来源广泛,易于回收利用,符合绿色化学和可持续发展的要求。
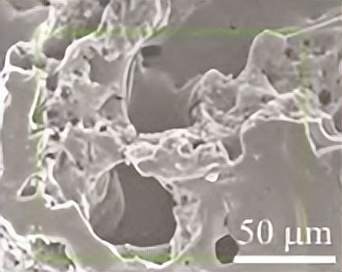
图.碳基质微观结构
2.技术优势
碳基臭氧催化剂的制备过程主要是通过杂原子掺杂、表面改性和缺陷工程使碳基质功能化。通过碳前体原位掺杂以化学方法将外来金属原子引入到碳骨架中,使原始碳的sp2电子构型发生改变,使之具有更加丰富的自由流动电子,碳材料边缘缺陷又能够介导电子,提升臭氧氧化体系中羟基自由基的产生效率。
多金属杂原子共掺杂
金属-杂原子共掺杂碳材料(具有更高的稳定性及催化活性。碳材料上引入杂原子有助于金属物种在碳材料上的锚定,同时,金属物质与引入的杂原子之间可能存在协同效应,进一步加强催化能力。过渡金属能够与碳基中不稳定的 C 形成 M-C 键,激活O3产生自由基。同时因为过渡金属的负载能够提高碳基的石墨化程度,有利于电子转移增强催化剂性能。在实际工程应用过程中,掺杂单一金属的一元催化剂无法表现出理想的催化能力,而多元催化剂能够发挥“1+1>2”的催化效果,科力迩的研究人员利用多种金属不同的-SA位点共存的优势,通过配对和/或远程耦合来改变彼此的协调环境,从而改变电子结构,以提高催化性能。
科力迩的研发人员将密度泛函理论应用到碳基多元金属原子催化剂的筛选,构建了一系列 AC-M(M=Cu、V、W、Mo、Fe、Zn、Co)结构,并测定其单位臭氧COD绝对去除量,有针对性的筛选出潜在的臭氧催化剂(|ΔGH*| 值接近 0 eV)。如下图2 介绍了其中一种钴镍双原子催化剂的制备过程,Ni 基催化剂对 C-C、C-O 和 C-H 键的裂解均具有较高的活性,Co 同样也对 C-C 键的断裂有活性。
通过调整不同比例的钴镍双金属比例,得到了最高的双位点密度,所制备的钴镍双原子催化剂表现出完全的双原子结构并获得优异的臭氧催化活性。Ni原子的引入改变了活性中心的电子构型并降低Co的 d 带中心,O-O 键在 Co-Ni 原子对位点上的断裂要容易,表明Ni和 Co 之间存在的协同效应对催化活性起到了正向的影响,同时也提高了非均相催化剂对碳沉积抵抗能力。通过DFT 计算,钴镍双原子催化剂能显著降低臭氧氧化中间体阶跃的相对自由能,表明钴镍双原子催化剂再弱碱性条件下具有优异的臭氧催化活性。
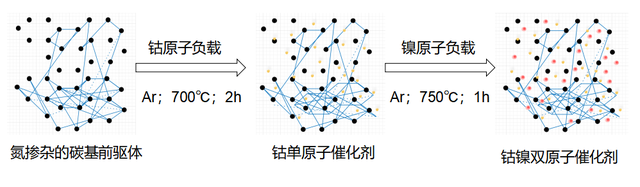
图2.钴镍双原子催化剂的制备过程
多金属合金催化剂之间的协同效应,不同种金属的掺杂原则如下:
1)添加的多种金属能提高催化剂的稳定性,减少纳米粒子团聚现象,达到提高催化活性的目的;
2)添加的多种金属能改变金属的电子特性和微观结构,使其提高了参与催化反应中间体的稳定性,从而提高催化活性;
3)多金属合金催化剂中不同金属之间电子的相互作用以及几何效应,能对纳米粒子起到了修饰的作用,从而提高催化活性。
稳定性好
碳基材料本身具有含有丰富的氮原子,N与碳的结构相似,因此很容易作为杂原子进行掺杂,在催化领域为研究新型催化剂提供了新的可能性。氮为反应物的最佳吸附提供了基础位置,同时具有良好的电子密度,由于氮的存在,使得活性相具有更好分散性和使得电子性质发生变化,因此可以提高催化性能。同时氮原子可以有效地锚定和稳固单金属原子,从而避免金属原子遭受到迁移和聚集,能够稳住高流动性金属原子,在热解过程中作为氮源形成强金属-氮配位键,极大地提高了材料的热稳定性和化学稳定性。
由于金属-氮配位相互作用更强,可以在高温下稳定金属-氮配位键,因此科力迩的研究人员在金属负载的过程中优选氮含量多的有机连接体(例如戊二醛286、乙二醛;环氧氯丙烷等其中的一种或多种),氨基与双醛以席夫碱的形式形成羧酰胺键,极大程度的改善了碳基材料的机械性能和热稳定性。同时通过有机交联剂的修饰为碳基体螯合金属离子提供更多的活性位点,增加了负载金属催化剂对金属的负载能力。金属-氮边界处具有复杂的络合结构,这些结构有助于金属成分与碳结构之间的 电荷传输,使得碳材料表面相互作用的局部区域具有更加密集的电子状态,从而具有更高的催化活性。形成的 C@N 键提高了对金属离子螯合效果,使得碳基臭氧催化剂的金属浸出风险大大降低,保证了碳基臭氧催化剂的安全性以及使用寿命。
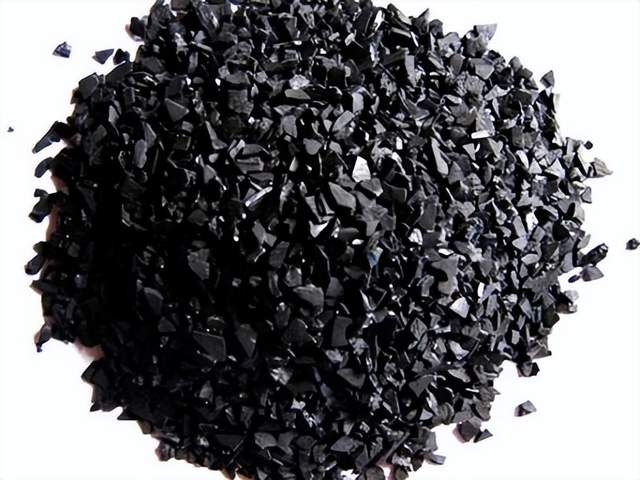
图.KHC-PC1001催化剂
成孔工艺
孔隙率是影响催化剂具有较高催化活性的一个至关重要的因素。高孔隙率和高表面积使反应分子易于进入活性物质。科力迩的KHC-PC1001型碳基臭氧催化剂使用的碳基体便具有多孔结后,其比表面积可超过1200 m2/g。为了避免金属离子的掺杂导致碳基体部分微孔堵塞,减小成品的比表面积,科力迩的研究人员采用了多种思路来解决这一难题。
其一,便是单次负载单一负载的多次烧结工艺,该工艺在保证金属均匀负载,最大程度增加氧化活性位点数量的同时,避免了金属聚集结团堵塞碳基体微孔的风险。
其二,便是在金属负载的过程中添加一定比例的水溶性致孔剂,例如(PEG,PVP,PVA 等。)水溶性致孔剂在催化剂材料制备中的工作原理主要是通过其在混合过程中的均匀分布和后续的去除,形成具有特定孔结构的催化剂,提高其催化效率。其在催化剂材料的制备过程中主要通过以下几个步骤发挥作用:
1)溶解与混合:水溶性致孔剂通常在水相中溶解,与其他组成材料(如金属盐、载体等)充分混合,形成均匀的胶体或溶液。
2)聚合与成型:在适当的条件下,这些混合物会通过加热、冷却、或者化学反应等方式形成固体基体。在这一过程中,水溶性致孔剂均匀分布在固体基体中。
3)去除致孔剂:在后续的处理过程中,例如干燥或煅烧,水溶性致孔剂会被去除。由于其水溶性,可以通过简单的水洗或高温煅烧使其挥发,从而在催化剂中形成孔隙。
4)孔结构的形成:致孔剂的去除留下一定的空间,形成多孔结构。这些孔隙能够提供较大的比表面积,有助于提高催化剂的活性和选择性。
5)催化性能优化:通过调节水溶性致孔剂的类型、浓度以及去除的方式,可以控制最终催化剂的孔径、孔容和分布,从而优化其催化性能。
其三,牺牲模版金属造孔法,利用可溶性的金属作为模版,在催化剂煅烧过程被去除被包裹在待制备材料周围,从而留下空腔或孔隙结构,例如在碳基臭氧催化剂的制备过程中,Co2+、Ni2+、Fe2+中的一种或几种金属分别随着Zn+一同负载在碳基体上,金属离子可以和连接体2-甲基咪唑进行配位并均匀分布于ZIF框架中,从而可以产生多金属ZIF。目标金属位点由2-甲基咪唑连接体和锌原子在空间上隔开,导致两者之间的空间距离变得更长。因此,在高温煅烧过程中ZIF骨架中的锌被蒸发掉后可以充当成孔剂, 从而产生大量的开放通道。
表.椰壳炭与KHC-PC1001不同孔隙比表面积贡献
通过以上三种方法,科力迩制备出的碳基臭氧催化剂比表面积超过1286 m2/g,在原有的碳基体基础上有所提升,通过碳基体与该型碳基臭氧催化剂的扫描电镜图也可看出,未经修饰的碳基体孔壁光滑,而该型号碳基臭氧催化剂的表面存在大量金属氧化物晶体,这些金属晶体分布均匀,对催化剂的比表面积,吸附性能以及空隙分布均有一定的提升
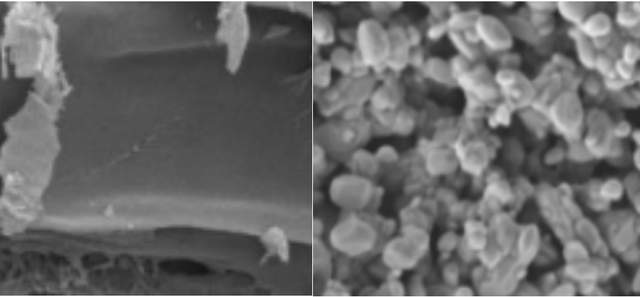
图.碳基体与KHC-PC1001的扫描电镜图(10000X)
(4)原位多段煅烧-退化工艺
高温煅烧过程对金属负载型催化剂的作用至关重要,它直接影响催化剂的物理化学性质和催化性能。煅烧过程可以去除杂质和形成晶体结构:煅烧可以去除原料中的水分和挥发性成分,去除毒素并防止金属聚集,从而恢复催化剂的活性。同时通过高温处理使无定形相转变为晶体相,改善催化剂的热稳定性、物理化学性能,并且增加其固定碳含量,从而满足产品要求。同时煅烧可以改变催化剂表面的酸性、比表面积等性质。煅烧还有助于金属与载体之间的相互作用,从而提高催化剂的整体性能。煅烧温度、煅烧时间、升温速度等是影响催化剂性能的关键因素。
1)煅烧温度:煅烧温度对催化剂的比表面积、孔隙结构和表面活性组分的分散度有显著影响。对于KHC-PC1001催化剂,700℃的煅烧温度能够获得最佳的选择性臭氧催化活性,因为在这一温度下,催化剂具有最大的比表面积和发达的孔隙结构。而当煅烧温度过高(如1000℃以上)时,催化剂表面会出现烧结现象,导致比表面积减少,不利于催化反应的进行。
2)煅烧时间:煅烧时间同样影响催化剂的物理化学性质。不足的煅烧时间可能导致催化剂前驱体未完全分解,活性组分无法充分形成或分散,从而影响催化剂的活性。而煅烧时间过长则可能导致催化剂烧结、比表面积减小、孔径塌陷等不利变化,降低催化剂的性能。例如,KHC-PC1001催化剂在700℃煅烧8小时后,表现出良好性能。
3)升温速度:升温速率的控制也对催化剂的性能有影响。过快的升温可能导致催化剂前驱体在达到最佳煅烧温度前未完全分解,而过慢的升温速率则会延长整个煅烧过程的时间,影响催化剂的最终性能。
综上所述,煅烧过程的优化对于制备高性能的金属负载型催化剂至关重要。通过控制煅烧温度、时间和升温速度,可以有效地调节催化剂的物理化学性质,从而提高其催化活性和稳定性。这些因素的优化需要根据具体的催化剂体系和应用需求来进行,科力迩的研究人员采取正交试验的方式,筛选出的最优的烧结条件,以确保催化剂在实际应用中达到最佳性能。
3、产品参数
表.KHC-PC1001型碳基臭氧催化剂和椰壳活性炭性能对比
产品优势
该型碳基臭氧催化剂的优势主要包括以下几点:
1)高比表面积:具有非常高的比表面积(约1300m2/g),这使得它能够提供大量的活性位点,提高催化效率。
2)多孔结构:多孔结构有助于提高活性组分的分散性,减少催化剂颗粒的团聚现象,从而提升催化活性和稳定性。
3)化学稳定性:材料具有良好的化学稳定性,可以在多种化学反应条件下保持结构不变,保证催化剂的长期使用。
4)机械强度:通常具有较好的机械强度,这有助于在反应过程中保持催化剂的完整性,减少磨损和破碎,年磨损率<2%。
5)可调节的孔径分布:通过不同的制备方法和后处理技术,可以调节孔径分布,以适应不同大小催化剂颗粒的需求。
6)易于回收和再生:在使用后可以通过简单的物理或化学方法进行回收和再生,便于重复使用,减少环境污染。
8)应用广泛:它们可以用于处理各种类型的工业废水,包括但不限于纺织、造纸、电子、制药和食品加工等行业,催化效果好、材料来源广泛,容易再生,环境友好,具有广阔的应用前景。
应用领域与案例分析
1)含油污水(油田采出水,压滤返排液、罐区切水、乳化酸性水)
具有优良的吸附性能,可吸附废水中的分散油、乳化油和溶解油。再利用其优越的臭氧催化性能可快速分解富集在催化剂表面的有机物,实现污水厂含油废水的深度处理。例如科力迩利用碳基臭氧催化剂处理新疆某石化含油废水,该含油废水先经隔油、气浮和生物处理,再用碳基臭氧催化剂进行深度处理。再臭氧投加量为100 ppm时,原水COD为180 mg/L,出水COD仅为23 mg/L,COD去除率超过90%;进水含油量35 ppm,出水含油量2.3 ppm。除此之外废水的含酚量从0.1 mg/L降至0.005 mg/L,含氰量从0.19 mg/L降至0.048 mg/L,COD从85 mg/L 降至18 mg/L。处理前后的水样图如下图所示。
碳基臭氧催化剂对油的吸附容量有限(一般为30~80 mg/g)),通常用作含油废水多级处理的最后一级处理,出水含油质量浓度可降至0.1~0.2 mg/L ,以达到深度净化的目的。
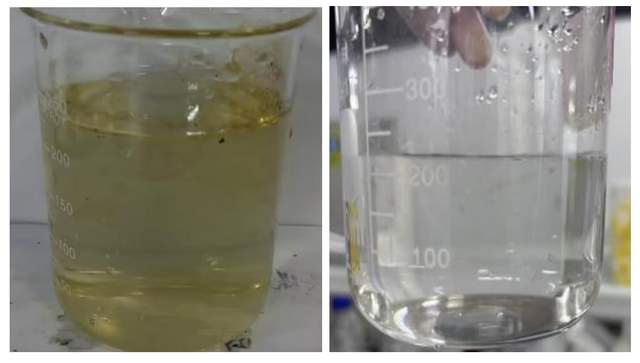
图.KHC-PC1001处理新疆某石化废水的效果对比(左进水,右出水)
2)垃圾渗滤液
垃圾渗滤液是在垃圾堆放和填埋过程中,由于微生物自身降解、雨雪冲刷等产生的黑棕色液体,具有有机物含量多、毒性大、异味大、地区差异大、难降解等特点,是一类成分复杂,难以生化降解的废水。科力迩科技公司针对垃圾渗滤液处理所研发的CDOF(Cyclonic Dissolved Ozone Flotation Unit)专利技术,装置内填充80%的KHC-PC1001,其反应原理是臭氧通入水中产生具有强氧化性的·OH,将垃圾渗滤液中难降解的大分子有机物氧化为易降解的小分子有机物,甚至矿化为CO2和H2O。CDOF具有反应速率快,设备简单、便于操作、无二次污染等优势,在垃圾渗滤液处理领域具有广泛前景。
科力迩全量化工艺处理浙江某垃圾填埋场老龄垃圾渗滤液,处理效果令人满意,该工艺对垃圾渗滤液的COD去除率超过80%,臭氧投加比仅为1.2左右,水质指标改善较大,处理前后水样对比明显。经过氧化处理后的浓缩液再回到污水厂的生化池处理,避免了污染物在污水系统中循环导致污水系统持续恶化的局面。该工艺处理深圳某垃圾渗滤液效果同样喜人,其处理前后对比如下图所示,进水COD约1500mg/L,经KHC-PC1001臭氧催化氧化工艺,20min出水400mg/L,40 min出水江COD降至200mg/L一下,废水B/C从0.22提升至0.37。同时,该技术不仅达到了全量化处理,还使污水厂运行更加稳定,也大幅降低了浓缩液处理成本。
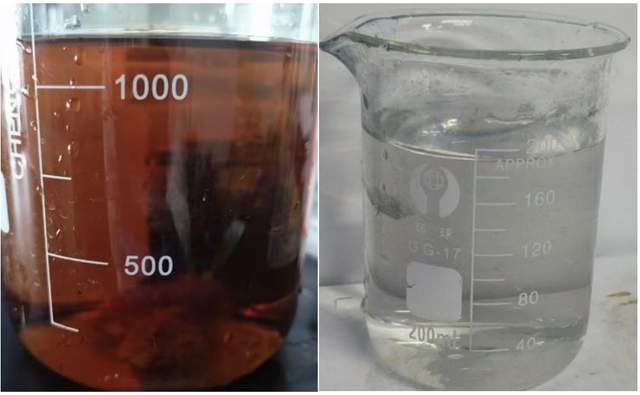
图.KHC-PC1001处理浙江某垃圾渗滤液前后对比(原水;出水)
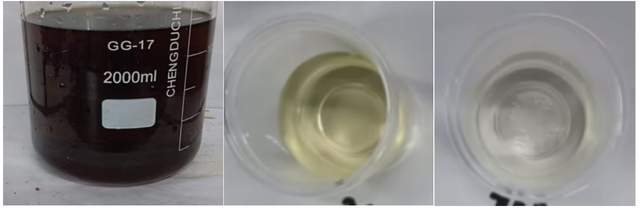
图.KHC-PC1001处理深圳某垃圾渗滤液前后对比(原水;20min出水;40min出水)
3)染料废水
染料废水成分复杂、水质变化大、色度深、浓度大,处理困难。处理方法主要有氧化、吸附、膜分离、絮凝、生物降解等。这些方法各有优缺点,其中活性炭能有效地去除废水的色度和COD。活性炭处理染料废水在国内外都有研究,但大多数是和其它工艺耦合,碳基臭氧催化剂对染料废水有良好的脱色效果。染料废水的脱色率随温度的升高而增加,而pH值对染料废水的脱色效果没有太大的影响。在最佳氧化工艺条件下,酸性品红、碱性品红废水的脱色率均>97%,出水的色度稀释倍数≤50倍,COD<50 mg/L,达到国家一级排放标准。
科力迩使用KHC-PC1001臭氧氧化工艺处理某工厂混合染料废水以及亚甲基蓝废水,其效果图如下图所示,混合染料废水中包括亚甲基蓝、甲基红、甲基橙、罗丹明等多种染料,色度>10000,TOC超过2000mg/L,经臭氧催化氧化处理后,臭氧投加量为200ppm时,脱色率超过99.9%,矿化率超过45%;亚甲基蓝废水色度>1000,TOC>500mg/L,在臭氧投加量为100ppm时,脱色率超过99.9%,矿化率超过47%。
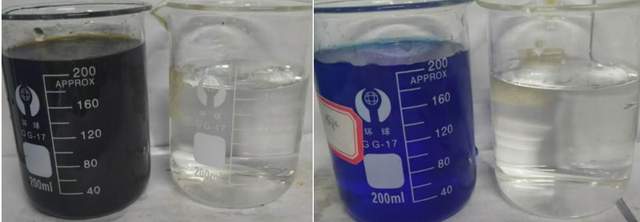
图.KHC-PC1001处理混合偶氮染料废水、亚甲基蓝染料废水效果图
科力迩碳基臭氧催化剂,独特的制备工艺,确保了催化剂表面拥有极高的活性位点密度,从而显著提升了催化效率。此外,科力迩还注重催化剂的稳定性与耐用性,通过特殊的表面处理与结构设计,有效延长了催化剂的使用寿命,降低了用户的使用成本。
与市面上的其他臭氧催化剂相比,科力迩碳基臭氧催化剂展现出了显著的优势。在催化效率方面,科力迩产品能够更快、更彻底地完成臭氧的生成与分解,为用户带来更高的生产效率与更优质的产品质量。在环保性能方面,科力迩催化剂在催化过程中几乎不产生任何有害物质,真正实现了绿色、环保的生产理念。
综上所述,科力迩碳基臭氧催化剂催化效率高、环保性能优秀,具有良好的应用前景。