硅铝基臭氧催化剂在污水处理中的应用
背景与需求分析
臭氧高级氧化技术是一种利用臭氧作为氧化剂来处理水中的有机污染物和微生物的技术。其应用原理主要基于臭氧的强氧化性,能够破坏有机物的化学结构,将其分解为无害的小分子物质。在水处理过程中,臭氧可以与水中的污染物发生直接反应,或者通过产生羟基自由基(·OH)等强氧化剂间接反应,从而达到净化水质的目的。
与传统水处理技术相比,臭氧高级氧化技术强氧化能力:
臭氧能够氧化多种有机和无机污染物,包括难以生物降解的物质;
反应速度快:与传统的化学处理方法相比,臭氧反应迅速,处理时间短;
无二次污染:臭氧在水中分解后主要生成氧气,不会产生有害的副产品;
提高水质:臭氧处理可以有效去除水中的色、嗅、味,提高水质的透明度和口感;
灵活性高:臭氧处理系统可以根据不同的水质和处理要求进行调整,具有很好的适应性;
减少消毒副产物:与氯消毒相比,臭氧处理可以减少三卤甲烷等消毒副产物的生成。
随着全球对环境保护和水质安全要求的提高,臭氧高级氧化技术因其高效、快速、环保等优势,在饮用水处理、工业废水处理、污水处理厂尾水深度处理等领域具有广阔的应用前景。
尽管臭氧高级氧化技术技术具有诸多优势,但其在实际应用中也存在一些缺陷,如臭氧利用率低、处理成本高、设备投资大等。为了克服这些缺陷,非均相臭氧催化技术应运而生。
非均相臭氧催化技术通过催化剂的引入,可以显著提高臭氧的利用率,降低处理成本,并提高反应速率。催化剂的存在可以促进臭氧分解产生更多的·OH,从而提高氧化效率。由于反应速率的提高,可以降低所需的臭氧和能量消耗,从而降低处理成本。非均相催化剂通常具有较好的稳定性和较长的使用寿命,减少了更换频率和维护成本。
科力迩研发的新型硅铝基臭氧催化剂KHC-F2001, 是提高反应效率、降低能耗的关键技术之一。该型催化剂采用了多种过渡金属氧化物(含贵金属)为催化组分,多段精准温控烧结技术,在保证活性的同时,提高催化剂的稳定性;在焙烧过程中辅以独特的成孔技术,制备的一种兼具高强度、高比表面积、高催化性能、耐酸碱且易于回收的硅铝基催化剂,而且在稳定性、选择性和环保方面表现出色,为水处理的可持续发展提供了新的动力。
随着全球对环境保护和水质安全要求的不断提高,臭氧催化剂在水处理行业中的市场需求日益增长。特别是在饮用水处理、工业废水处理、污水处理厂尾水深度处理等领域,臭氧催化剂具有广阔的应用前景。
科力迩硅铝基臭氧催化剂(KHC-F2001)
硅铝基催化剂是一类广泛应用于石油化工领域的催化剂,主要由硅和铝的氧化物组成。这类催化剂具有较高的比表面积、良好的热稳定性和酸性,使其在催化裂化、烷基化、异构化等反应中表现出色。硅铝基催化剂的制备方法主要包括溶胶-凝胶法、水热合成法和微乳液法等。科力迩的研发人员采用溶胶-凝胶法,通过控制硅源和铝源的配比、水解和缩聚反应条件,可以制备出不同孔结构和酸性的硅铝基催化剂,从中筛选出最优的硅铝基臭氧催化剂-KHC-F2001,其外观为红色球状颗粒如下图所示。
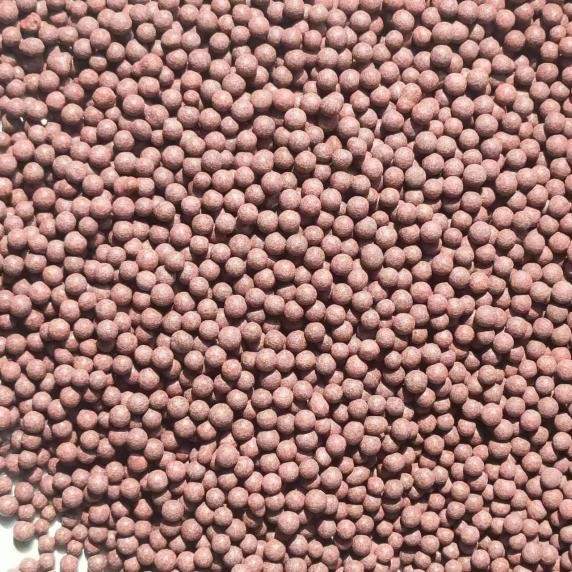
图.科力迩KHC-F2001催化剂外观图
为了保证催化剂的催化活性和稳定性,KHC-F2001经过了改性处理,科力迩的研发人员通过金属离子掺杂、酸处理、热处理和表面修饰等改性方法,调节了硅铝基催化剂的酸性、孔结构和表面性质,从而满足不同反应的需求。该催化剂的活性中心主要是酸性位点,包括路易斯酸位和布伦斯德酸位。这些酸性位点可以促进反应物的吸附、活化和转化,从而提高反应速率和选择性。此外,KHC-F2001的表面性质和孔结构也对其催化性能有重要影响。
技术优势
1.贵金属沉积
贵金属如铂(Pt)、钯(Pd)、铑(Rh)、银(Ag)等,由于其独特的电子结构和表面特性,能够有效地促进反应物的吸附和活化,加速反应速率。这意味着在相同的反应条件下,掺杂了贵金属的催化剂能够更容易地启动催化反应,从而提高反应速率和效率,科力迩的研发人员在针对石油化工、煤化工、医药废水等多种废水处理应用中得到了验证。
经过长期的试验论证,KHC-F2001掺杂贵金属之后具有多方面的优势,首先,掺杂可以显著提高催化剂的活性,使得反应在更低的温度或压力下进行,从而节约能源。其次,掺杂可以增强催化剂的选择性,减少副反应的发生,提高目标产物的产率。此外,掺杂贵金属还可以提高催化剂的稳定性,延长其使用寿命,减少更换频率和维护成本。掺杂贵金属提高催化剂性能的机理主要包括以下几点:
电子效应:贵金属的掺杂可以改变催化剂表面的电子结构,增强催化剂表面的电子密度或电子缺失,从而提高催化活性位点的反应能力。
几何效应:贵金属的引入可能会改变催化剂的表面结构,例如形成更多的活性位点或优化活性位点的几何构型,从而提高催化效率。
多金属协同作用:贵金属与基体金属之间可能存在协同作用,这种相互作用可以促进反应物的吸附和活化,以及产物的脱附,从而提高催化性能。
热稳定性:贵金属的掺杂有助于提高催化剂的热稳定性,使其在高温条件下仍能保持良好的催化性能。
抗中毒能力:掺杂贵金属可以提高催化剂的抗中毒能力,减少反应过程中可能产生的毒物对催化剂活性的影响。
以铂为例,科力迩的研发人员将铂引入到KHC-F2001后,大大丰富了催化剂的表面活性位点,这些活性位点能够吸附氧气分子,并通过电子转移过程促进氧气分子的解离,生成活性氧物种。这些活性氧物种是臭氧生成的关键中间体,它们能够进一步与有机污染物发生反应,从而提高催化剂对有机污染物的氧化效率。此外,铂的引入还可以改善催化剂的热稳定性,减少催化剂在高温条件下的烧结和失活,从而延长催化剂的使用寿命。同时,铂的高选择性可以减少副反应的发生,提高目标产物的产率。综上所述,铂的引入通过提供更多的活性位点、改善电子结构、增强吸附能力以及提高热稳定性等机制,显著提升了臭氧催化剂的性能。
2.多段精准控温烧结技术
科力迩多段精准控温烧结技术在制备臭氧催化剂方面具有显著优势。该技术通过精确控制烧结过程中的温度,能够优化催化剂的微观结构,从而提高其催化效率和稳定性。温度对臭氧催化剂性能的影响主要体现在以下几个方面:
首先,温度影响催化剂的活性组分分布。在特定的温度下,催化剂中的活性组分能够均匀分散,形成更多的活性位点,从而提高催化效率。例如,某些金属氧化物催化剂在中低温烧结时,活性组分分布较为均匀,能够有效催化臭氧的分解。温度影响催化剂的晶粒大小。适当的烧结温度可以促进晶粒的生长,但过高的温度会导致晶粒过度生长,减少活性表面积,降低催化活性。例如,银基催化剂在400℃至500℃的温度范围内烧结,可以得到适宜大小的晶粒,展现出最佳的臭氧催化性能。
同时温度还会影响催化剂的热稳定性。适当的烧结温度有助于形成稳定的晶体结构,提高催化剂的耐热性能,从而在高温条件下仍能保持良好的催化活性。例如,锰基催化剂在600℃至700℃的温度下烧结,可以形成稳定的尖晶石结构,有效提升其在高温下的臭氧催化性能。科力迩的研究人员基于催化剂的胚体与活性组分组成,经过数千次的试验,得出了KHC-F2001最优的烧结程序,通过多段精准控温烧结技术通过精确控制烧结过程,使催化剂在特定温度下展现出最佳的臭氧催化性能,稳定性以及强度等。
3.高比表面积
高比表面积对于臭氧催化剂的催化性能至关重要,因为它直接关联到催化剂表面活性位点的数量,从而影响催化效率和反应速率。比表面积越大,催化剂表面可用于反应的活性位点越多,这有助于提高催化反应的转化率和选择性。
科力迩的KHC-F2001催化剂的比表面积约250-300 m2/g,而市面上同类催化剂的比表面积仅为50-100 m2/g;KHC-F2001超高的比表面积主要得益于其独特的喷雾造粒方法;粗细相配的原料组成,科力迩研发人员精心设计了硅铝比例和其它成分的配比,以确保在烧结过程中形成多孔结构;多管齐下的造孔技术以及对烧结程序的精密把控,促进微孔的产生。
科力迩的研究人员在开发高比表面积催化剂时,面临的一个主要挑战是如何在提高比表面积的同时保持催化剂的机械强度。为了达到这一目标,研究人员需要精心设计催化剂的配方和制备工艺。这包括选择合适的前驱体和成孔剂,优化烧结条件,以及可能的后处理步骤来增强催化剂的结构稳定性。此外,研究人员还需要进行大量的实验来测试不同条件下的催化剂性能,既要保证了催化剂的机械强度,又避免了过度烧结导致的孔隙坍塌,从而在强度与比表面积之间取得了平衡,以找到最佳的平衡点。这一过程需要高度的专业知识和细致的实验操作,以确保催化剂在实际应用中既具有高活性又具有足够的机械强度。
通过这些综合措施,科力迩成功研发出既具有高比表面积又保持良好机械强度的硅铝基臭氧催化剂,有效提升了催化性能。
4.超亲水改性对催化性能的提升
为了进一步提升KHC-F2001性能,使其在面对复杂的水质时依旧具有长期稳定的催化效果,科力迩使用了先进的原子沉积技术对该催化剂进行了超亲水改性:首先对催化剂表面进行清洁和活化处理,以确保表面具有足够的活性位点,便于后续原子沉积。通过物理或化学气相沉积方法,在催化剂表面沉积一层或多层具有超亲水性的原子或分子。这通常涉及使用特定的前驱体气体,在一定温度和压力条件下,使原子或分子在催化剂表面形成均匀的薄膜。沉积完成后,可能需要进行热处理以增强沉积层与催化剂基体之间的结合力,并优化超亲水层的结构和性能。最后,对改性后的催化剂进行性能测试,以评估其超亲水性能和催化活性。
科力迩的超亲水改性技术会改变KHC-F2001表面的化学组成和结构,从而降低表面能,增加表面的亲水性。原子沉积形成的超亲水层可能会增加催化剂表面的粗糙度,从而提供更多的活性位点和反应界面。超亲水层中含有羟基、羧基等亲水性功能团,这些功能团能够与水分子形成氢键,增强催化剂表面的亲水性。经过精密的测试以及长期的试验论证,科力迩的超亲水该新技术对催化剂性能提升的影响主要体现在以下几个方面:
提高催化活性:超亲水表面可以促进反应物在催化剂表面的吸附和扩散,从而提高催化反应的速率和效率。
增强选择性:超亲水改性有助于提高催化剂对特定反应的选择性,减少副反应的发生。
延长使用寿命:超亲水层可以保护催化剂表面不受污染和毒化,从而延长催化剂的使用寿命。
提升稳定性:超亲水改性有助于稳定催化剂的表面结构,使其在各种反应条件下都保持较高的活性和稳定性。
超亲水改性能够显著提升催化剂的性能,使其在工业应用中表现出更好的催化效果。
产品参数
表.KHC-PC2001的性能参数
产品优势
科力迩研发的KHC-PC2001催化剂具有以下优势:
1)强度高:KHC-PC2001具备良好的机械强度,受压强度>150N/粒,能够承受工业反应过程中的物理应力,延长使用寿命。
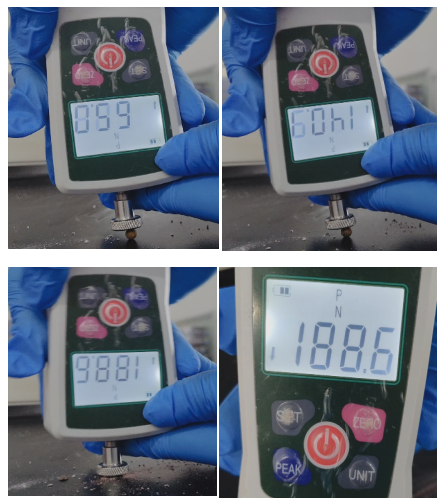
图.KHC-PC2001催化剂强度测试结果
2)高效催化性能:该催化剂能够有效降低臭氧分解所需的活化能,从而提高催化效率,加速污染物分解的过程。经实验论证,科力迩的KHC-PC2001在工业废水处理中的应用,可比市面上同类型的催化剂提高臭氧利用率20%以上,这意味着在相同条件下,使用该催化剂可以更快地降低废水中的有机污染物浓度,提高处理效率。
3)比表面积大:KHC-PC2001的多孔结构有助于提高活性组分的分散性,减少催化剂颗粒的团聚现象,高比表面积意味着更多的活性位点暴露于反应物,从而提高催化效率。
4)活性位点丰富:丰富的活性位点能够促进更多的化学反应,提高反应速率和选择。
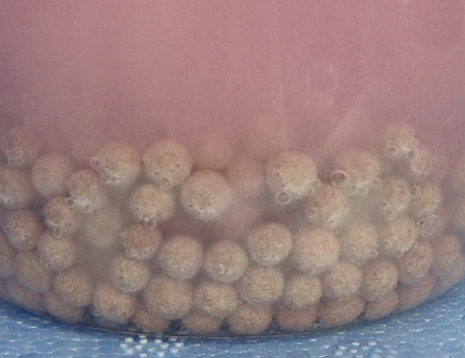
图.KHC-PC2001在使用过程中将有机物氧化为二氧化碳产生丰富的微气泡
5)不易堵塞,抗中毒能力强:由于KHC-PC2001结构特性,该催化剂不易被反应生成物堵塞,保持了良好的催化活性;且KHC-PC2001硅铝基催化剂对有机物、重金属等污染物具有较强的抗中毒能力,不易被污染,使用寿命长。
6)耐磨耐酸碱:KHC-PC2001具有良好的化学稳定性,能够抵抗磨损和酸碱环境的侵蚀;同时具有良好的热稳定性和化学稳定性,能够在较宽的温度和pH范围内保持催化活性,不易失活。如下图,科力迩的研发人员利用振荡以及酸碱溶液浸泡的方式测试催化剂的耐磨耐酸碱性能,在300r/min,震荡24h的条件下,KHC-PC2001的磨损率仅为0.13%;在pH=3、pH=12的酸碱溶液中浸泡12 h,催化剂无碎裂,金属析出,表明KHC-PC2001耐磨性能良好、能够轻松应对强酸强碱环境、稳定高效、安全可靠。
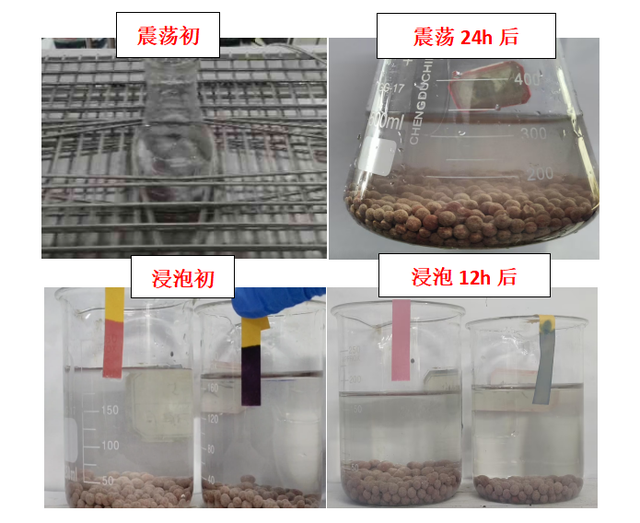
图.催化剂耐磨性能、耐酸碱性能测试
7)易于回收:KHC-PC2001物理性质使其在使用后容易从反应体系中分离和回收,便于循环使用。
8)应用广泛:KHC-PC2001适用于多种化学反应,包括石油化工、精细化工、制药食品等行业,具有广泛的应用前景。
应用领域与案例分析
1)老龄垃圾渗滤液处理
老龄垃圾渗滤液,作为垃圾填埋场长期运营后产生的复杂废水,其特性分析是科力迩非均相臭氧催化技术应用的基石。这类渗滤液通常具有高浓度有机物、重金属离子、氨氮及难降解物质等特点,其化学需氧量(COD)可高达数万毫克升,远超一般工业废水处理标准。此外,老龄渗滤液的pH值波动大,色度高,且含有大量微生物代谢产物,处理难度极大。
科力迩注重将先进技术与实际应用相结合,通过不断优化处理工艺流程和设备选型配置,实现了老龄垃圾渗滤液的高效处理。公司承建的多个处理项目均取得了显著成效,例如下图是KHC-PC2001处理福州某垃圾渗滤液前后对比,进水COD约3000 mg/L、总氮约150 mg/L,pH为7左右,该废水色度高、可生化性差生化处理难以达标。经KHC-PC2001臭氧催化氧化工艺处理后,30min后出水COD降至200 mg/L以下、总氮将至60 mg/L,出水澄清透明,可生化性提高。同时,该技术不仅达到了全量化处理,还使污水厂运行更加稳定,也大幅降低了浓缩液处理成本。

图. KHC-PC2001处理福州某垃圾渗滤液前后对比(进水;出水)
使用KHC-PC2001处理漳州某垃圾渗滤液前后对比,进水COD约400 mg/L,色度>500,值得注意的是,该地产生的垃圾渗滤液盐含量极高(>30000mg/L),传统生化无法处理该类废水,使用科力迩非均相臭氧氧化工艺处理处理该废水,停留时间仅为30 min,出水COD<60mg/L,色度降低至5以下。在采用科力迩非均相臭氧催化技术后,该垃圾填埋场的渗滤液处理效率提高了30%,同时能耗降低了20%,为项目方带来了显著的经济效益和环境效益。据实验数据显示,科力迩自主研发的KHC-PC2001在高盐度废水连续运行数千小时后,其催化效率仍能保持在90%以上,这一成果在行业内处于领先地位。
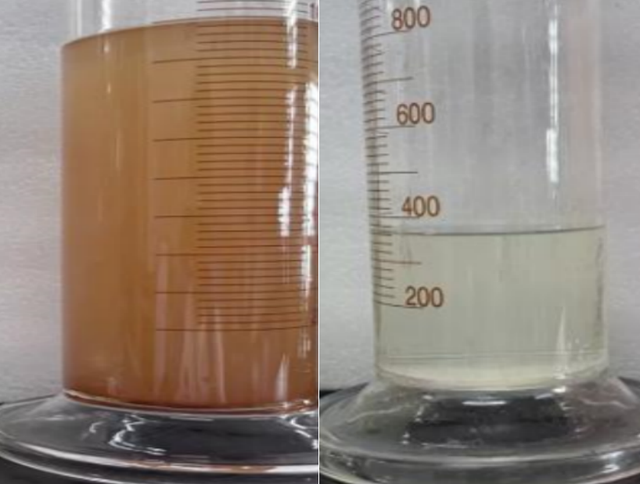
图. KHC-PC2001处理漳州某垃圾渗滤液前后对比(进水;出水)
2)医药废水处理
据国家环保部门统计,医药工业作为高污染行业之一,其废水排放量占全国工业废水排放总量的相当比例,且废水中含有大量难降解的有机物、重金属离子及生物毒性物质,对水体环境构成严重威胁。若不经有效处理直接排放,将严重破坏生态平衡,影响人类健康。以内蒙古某大型制药企业为例,其生产过程中产生的废水COD(化学需氧量)浓度高达数千毫克升,远超国家排放标准。该企业曾尝试采用传统生物处理工艺,但处理效果有限,难以达到环保要求。
在此背景下,科力迩利用独家的臭氧催化氧化工艺处理医药废水取得了较好的效果,其进出水的对比图如下图所示,医药废水呈褐色,不仅浓度高,色度大还具有一定的生物毒性,经过科力迩以KHC-PC2001为核心的非均相臭氧氧化工艺处理后,在停留时间仅为15min的条件下,出水澄清透明,COD降至200mg/L以下,出水悬浮物将至20mg/L,B/C也从0.1以下提升至0.37,为该类废水的处理提供了新的思路。
图.利用KHC-PC2001处理内蒙古某医药废水
科力迩硅铝基臭氧催化剂,作为行业领先的环保解决方案,凭借其卓越的性能和独特的优势,在众多硅铝基臭氧催化剂中脱颖而出。高效催化性能、长寿命与低流失率、深度氧化能力、加压催化反应、均相与非均相催化氧化、水力空化催化等多段、多维度、多重催化氧化反应过程相互协同,确保了处理效果的稳定性和可靠性。相比市面上单一催化方式的催化剂,我们的产品具有更高的处理效能和适应性。